RS1600i ARB fitting
#42
Wye Valley Hardcore

Muz - Sounds a good idea, 18 OR 20mm diameter rear arb would be the ticket - with the mounting bushes milled/drilled out to accomodate it. Rose jointed links... Not sure how i'd attach them to the bar, weld i guess - never used them before! I have a TIG welder available so that could open up some possibilities...?
Was thinking of making a thicker front ARB to replace my S2 item...
Was thinking of making a thicker front ARB to replace my S2 item...
With regards to the front, an RS1600i set up is all you ever need. Maybe some oversized rosejointed tie arms if your serious but it's not too important.
#44
Wye Valley Hardcore

You just have a short tube with a Rose joint either end, same as the longer arms. I'd probably cut the original mounts off the existing ARB then weld a flat section of steel about 20mm x 40mm with a hole to bolt the drop link through.
#45
PassionFord Post Troll
iTrader: (7)
Join Date: Feb 2005
Location: shrewsbury shropshire
Posts: 2,864
Likes: 0
Received 2 Likes
on
2 Posts

I didnt think about needing a TIG welder so that puts that out of the question, if T45 is expensive then maybe CDS is the route to go down.
Those joints are Ł5 each?? Surely they cant be that good if the usual price for a decent joint is Ł30??
Gus where did you get your adjustable rear ARB? ive got a MK4 popular which doesnt have a rear ARB at all so what would i need to fit one im assuming the rear setup from a RS if i cant find an adjustable item.
Those joints are Ł5 each?? Surely they cant be that good if the usual price for a decent joint is Ł30??
Gus where did you get your adjustable rear ARB? ive got a MK4 popular which doesnt have a rear ARB at all so what would i need to fit one im assuming the rear setup from a RS if i cant find an adjustable item.
have look through his shop he makes and sells everythin i need to make adj rear arms
http://www.ebay.co.uk/itm/Turnbuckle...item255c44c476
#46
It Wasnt Me!

I would not want to use ally if possible as I don't have access to a TIG welder which would make it not so much of a budget set up having to get the lads at AH to weld them all up. I would think T45 would still also be very expensive. You would need 10 rose joints at about Ł30 a peice which is where the cost comes in.
You wouldn't need to weld anything if you used ally, that's the whole point, and the weight saving over steel!
I wouldn't touch a cheap rose joint, i've priced GOOD (i.e. proper) rose joints for this setup before and im sure they were Ł40-50 a piece which made it expensive and put me off back then.
I've got one ally rear link bar made up in my boot, i'll take a pic tomorrow, its not the right length as it was for a wider setup.
other option is to chop the rear wihbones about and fabricate them to take rose joints to make them adjustable, and then you could keep the standard spring/shock setup.
#47
Wye Valley Hardcore

You'd still need to weld Ally? How else would you have a mount for the drop links attatched to the front tie bars and attach the end bungs with the threads for the rose joints? Unless the tube sidewalls were thick enough to directly thread which would mean using thick wall tube and make it heavier anyway. The weight saving comes as ally is a far lighter material than Mild steel, not the fact it has less welds.
#48
It Wasnt Me!

What? I'm talking about replacing the rear wishbones to make adjustable?
I've got one bar made up, it's not THICK and it's threaded. will post pics tomo, no welding at all needed for the rear end unless you wanted to keep the rear ARB....even then you could make up a clamp
I've got one bar made up, it's not THICK and it's threaded. will post pics tomo, no welding at all needed for the rear end unless you wanted to keep the rear ARB....even then you could make up a clamp
#50
Wye Valley Hardcore

What? I'm talking about replacing the rear wishbones to make adjustable?
I've got one bar made up, it's not THICK and it's threaded. will post pics tomo, no welding at all needed for the rear end unless you wanted to keep the rear ARB....even then you could make up a clamp
I've got one bar made up, it's not THICK and it's threaded. will post pics tomo, no welding at all needed for the rear end unless you wanted to keep the rear ARB....even then you could make up a clamp
So am I? Like this?
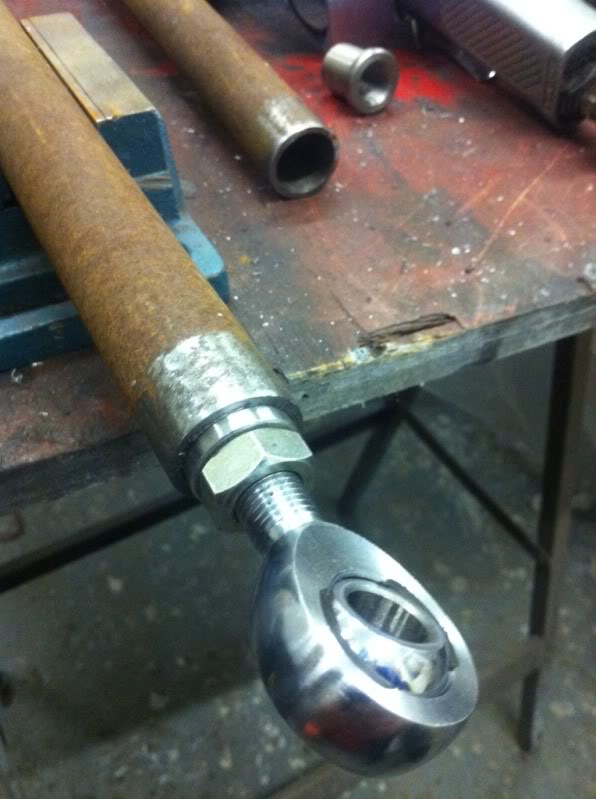
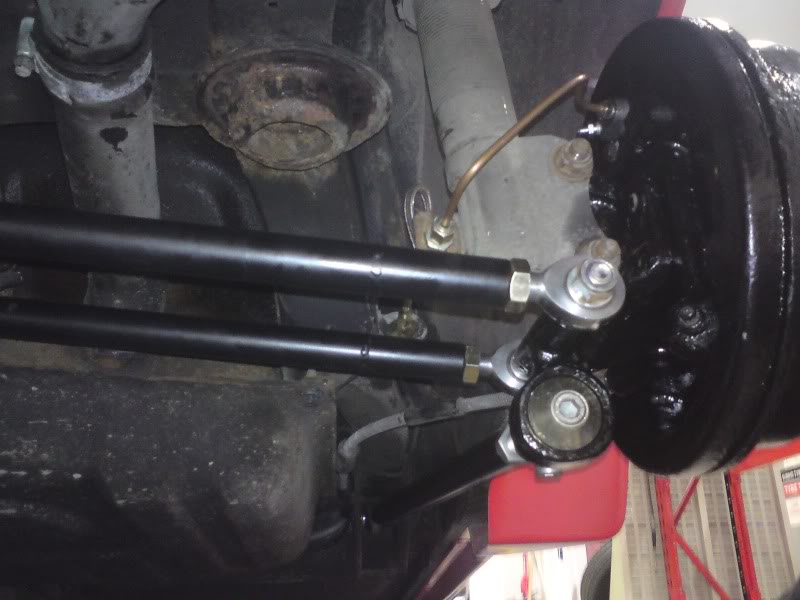
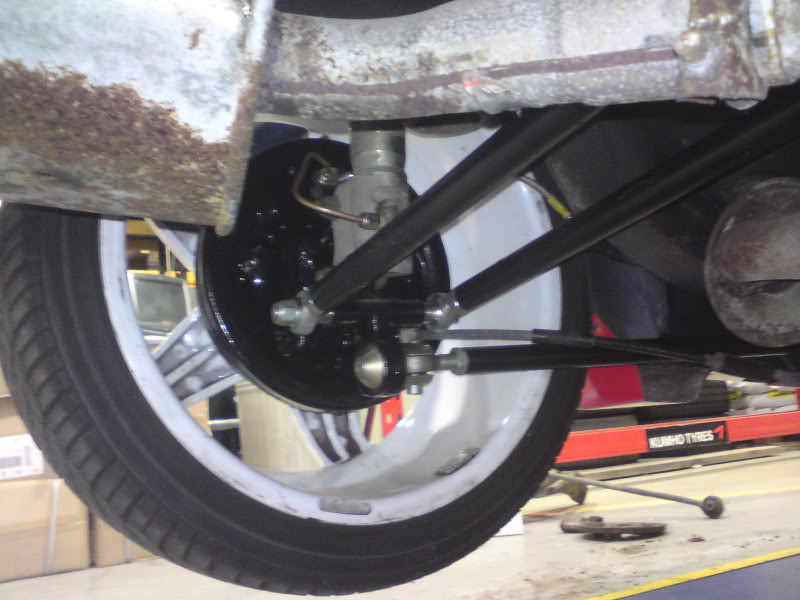
Have you got a pic as I'm a little confused? They could be made out of Alloy and be lighter, but as far as I can work out certain bits would need to be welded? You could run a thread into the end of the ally tube itself, but I wouldn't trust a suspension componant under strain to be a thread in thinwall ally tube? Obviously it depends on what grade of ally you use but then the cost would go through the roof.
The above link arms use mild steel with threaded steel inserts which are then welded into the bars. Thsi is the way I was going to make mine, anyway.
#51
Wye Valley Hardcore

No, all the MEF ones I've seen don't, but I've heard a few people, inc. Gus say that it needs one and the car rolls too much under hard cornering. Has your MEF set up got threaded inserts or is the tube itself threaded?
#53
PassionFord Post Whore!!
iTrader: (4)

Some of the pics at the bottom of this page are porn:
http://www.rs1600i.net/index.php?view=brooklyn
Love that car. The data post rs1600i uses a similar rear arb setup too.
Rob,
http://www.rs1600i.net/index.php?view=brooklyn
Love that car. The data post rs1600i uses a similar rear arb setup too.
Rob,
#54
Wye Valley Hardcore

Cracking pictures there, Rob. I love that car. The graphics are spot on. I was also told that the Group A cars didn't use the same Ledas as I have, but those photos have confirmed they did, which makes me happy.
#55
It Wasnt Me!

So am I? Like this?
Have you got a pic as I'm a little confused? They could be made out of Alloy and be lighter, but as far as I can work out certain bits would need to be welded? You could run a thread into the end of the ally tube itself, but I wouldn't trust a suspension componant under strain to be a thread in thinwall ally tube? Obviously it depends on what grade of ally you use but then the cost would go through the roof.
The above link arms use mild steel with threaded steel inserts which are then welded into the bars. Thsi is the way I was going to make mine, anyway.
Have you got a pic as I'm a little confused? They could be made out of Alloy and be lighter, but as far as I can work out certain bits would need to be welded? You could run a thread into the end of the ally tube itself, but I wouldn't trust a suspension componant under strain to be a thread in thinwall ally tube? Obviously it depends on what grade of ally you use but then the cost would go through the roof.
The above link arms use mild steel with threaded steel inserts which are then welded into the bars. Thsi is the way I was going to make mine, anyway.
Which parts exactly do you think would need to be welded if made from ally? I'm not talking about tube i'm talking about solid aluminium bar, drilled and tapped, I think that's where we've got our wires crossed

I never got a chance to take a pic today but will try tomorrow, I'd imagine it would be stronger than the original setup as its only thin steel with a rubber bush/metal insert holding it all together, plus the inner wishbone mount isn't exactly substantial, the ally bar I have is solid and I doubt the threads would be any kind of issue from a strength pov.
Last edited by vroooom ptssssh; 20-10-2011 at 09:05 PM.
#56
Wye Valley Hardcore

Ahhh ally BAR I thought you meant TUBE with inserts. I'm not good with different grades of ally and the cost/strength but I imagine the ally would have to be a very good/expensive type to be safe and hold a thread? I've priced a set of steel ones up for me to make at around Ł400, I aint paying more than that

#57
PassionFord Post Whore!!
iTrader: (4)

What grade of ali is it mate? Strength can and will be a major issue depending on material grade.
I know mate its a quality car, i think leda remade the suspension for him (if i skim read the description), sounds awesome in the vid too 
Would love to read some of the suspension set up notes, that hinted at why the pivot point for the rear arms had been changed etc.
Question,
Does an adjustable length trailing arm allow for good adjustment of toe in/out? Rather than just moving the wheel forward/backward...?
Cheers
Rob,
Cracking pictures there, Rob. I love that car. The graphics are spot on. I was also told that the Group A cars didn't use the same Ledas as I have, but those photos have confirmed they did, which makes me happy.

Would love to read some of the suspension set up notes, that hinted at why the pivot point for the rear arms had been changed etc.
Question,
Does an adjustable length trailing arm allow for good adjustment of toe in/out? Rather than just moving the wheel forward/backward...?
Cheers
Rob,
#58
Wye Valley Hardcore

What grade of ali is it mate? Strength can and will be a major issue depending on material grade.
I know mate its a quality car, i think leda remade the suspension for him (if i skim read the description), sounds awesome in the vid too
Would love to read some of the suspension set up notes, that hinted at why the pivot point for the rear arms had been changed etc.
Question,
Does an adjustable length trailing arm allow for good adjustment of toe in/out? Rather than just moving the wheel forward/backward...?
Cheers
Rob,
I know mate its a quality car, i think leda remade the suspension for him (if i skim read the description), sounds awesome in the vid too

Would love to read some of the suspension set up notes, that hinted at why the pivot point for the rear arms had been changed etc.
Question,
Does an adjustable length trailing arm allow for good adjustment of toe in/out? Rather than just moving the wheel forward/backward...?
Cheers
Rob,
#59
Wye Valley Hardcore

Originally Posted by Website
the current spring poundage is 1000 on the rear and 350 on the front, in the spares there are 16 sets ranging from 250 lbs to 1200 lbs for both front and rear
#60
It Wasnt Me!

I'm not too good with grades myself, I'd need to speak to the chap that machined this bar up, he originally made a set for a mk3 escort race car but the project got scrapped and he gave me this bar as a template (its no use to me for anything other than as this car had a wider track) I can't remember what grade but will see if i can find out.
He said it was cheaper and easier/faster to do with this suff, and at first I did question strength but he assured me it wouldnt be an issue, otherwise it wouldn't have been used for a race car.....
it doesnt appear to be your typical ally bar though.
IIRC, with proper good quality rose joints when I priced it up, the rose joints alone came to Ł450 ish! 10x rose joints a Ł45ish ea. 4 LH thread, 6 RH. then you've got the machining of the inserts.....lot of work on the lathe inc machining the bars but would have saved loads as would do it myself, but factor in 2 gaz coilovers and your talking a few hundred quid! You can get cheap rose joints, but they always have some play and wear out quickly, shite in other words!
He said it was cheaper and easier/faster to do with this suff, and at first I did question strength but he assured me it wouldnt be an issue, otherwise it wouldn't have been used for a race car.....
it doesnt appear to be your typical ally bar though.
IIRC, with proper good quality rose joints when I priced it up, the rose joints alone came to Ł450 ish! 10x rose joints a Ł45ish ea. 4 LH thread, 6 RH. then you've got the machining of the inserts.....lot of work on the lathe inc machining the bars but would have saved loads as would do it myself, but factor in 2 gaz coilovers and your talking a few hundred quid! You can get cheap rose joints, but they always have some play and wear out quickly, shite in other words!
Last edited by vroooom ptssssh; 20-10-2011 at 09:45 PM.
#61
PassionFord Post Whore!!
iTrader: (4)

As a quick example, yield strength of mild steel is around 54,000 psi (for an average grade like 1018),
Ali - 6061 is a common grade and has a yield strength of about 8000, 6061-t6 which isn't amazingly cheap and still only has a yield of around 40,000 psi......
Im not sure what sort of loads these suspension parts will be under.... plus a decent safety margin, be nice to roughly work out before plunging ahead.
Rob,
Ali - 6061 is a common grade and has a yield strength of about 8000, 6061-t6 which isn't amazingly cheap and still only has a yield of around 40,000 psi......
Im not sure what sort of loads these suspension parts will be under.... plus a decent safety margin, be nice to roughly work out before plunging ahead.
Rob,
#62
PassionFord Post Whore!!
iTrader: (4)

I would have thought so. to have the back wheel toe-ing in, say, could you also shorten the front two wishbone arms and shorten the trailing arm to pull the hub in slightly?
Rob,
#63
I'm Finding My Feet Here Now
Thread Starter
Join Date: Nov 2009
Location: Hertfordshire
Posts: 101
Likes: 0
Received 0 Likes
on
0 Posts

This thread is moving very rapidly!!
Ok so theres been a lot of talk on what grade of steel/aluminium would need to be used and then how expensive it is going to be to obtain. I have a friend who works for a company who design and develop mechanisms used on spacecraft and has access to aircraft grade aluminium so im gonna ask him to shed some light on what grades he uses and whether or not they will be useful for the job in hand and finally whether or not he can get it in tube form.
Depending on whos serious about trying to get these made up surely we could a discount on some good quality rosejoints if we bought them in bulk??
The question i have is if i were to run the adjustable rear linkage what arb would be used and how would it be fitted?? I have a MK4 popular so i dont have a rear arb to start with.
This might be a stupid question but is there any alternative to using rosejoints??
Ok so theres been a lot of talk on what grade of steel/aluminium would need to be used and then how expensive it is going to be to obtain. I have a friend who works for a company who design and develop mechanisms used on spacecraft and has access to aircraft grade aluminium so im gonna ask him to shed some light on what grades he uses and whether or not they will be useful for the job in hand and finally whether or not he can get it in tube form.
Depending on whos serious about trying to get these made up surely we could a discount on some good quality rosejoints if we bought them in bulk??
The question i have is if i were to run the adjustable rear linkage what arb would be used and how would it be fitted?? I have a MK4 popular so i dont have a rear arb to start with.
This might be a stupid question but is there any alternative to using rosejoints??
#65
Wye Valley Hardcore

Weight. To be able to tap directly into the tube it would need to be thickwall to get any proper strength which would weigh alot more than using inserts. If using aluminium, I would guess it would have to be bar rather than tube for overall strength. I don't think affordable ally tube would be strong enough.
#67
Wye Valley Hardcore

What we ideally need is someone with a set to give us all the dimentions of the tubes inc length, wall thickness and diameter, rose joint size and grade, whether they are reft or right hand threaded and make our lives easier

Do yours have a left hand thread on one end and a right on the other then you turn the bar itself, on two flat sections say, to legthen and shorten then lock it off with the nuts?
#68
PassionFord Post Whore!!
iTrader: (4)

However, the majority of a cylinders stiffness comes from or near the surface, so removing half the volume of the rod from the centre will not half the stiffness etc.
Also remember that when drilling and tapping you have essentially created a thin walled tube.... it will deform/break here.
s This thread is moving very rapidly!!
Ok so theres been a lot of talk on what grade of steel/aluminium would need to be used and then how expensive it is going to be to obtain. I have a friend who works for a company who design and develop mechanisms used on spacecraft and has access to aircraft grade aluminium so im gonna ask him to shed some light on what grades he uses and whether or not they will be useful for the job in hand and finally whether or not he can get it in tube form.
Depending on whos serious about trying to get these made up surely we could a discount on some good quality rosejoints if we bought them in bulk??
The question i have is if i were to run the adjustable rear linkage what arb would be used and how would it be fitted?? I have a MK4 popular so i dont have a rear arb to start with.
This might be a stupid question but is there any alternative to using rosejoints??
Ok so theres been a lot of talk on what grade of steel/aluminium would need to be used and then how expensive it is going to be to obtain. I have a friend who works for a company who design and develop mechanisms used on spacecraft and has access to aircraft grade aluminium so im gonna ask him to shed some light on what grades he uses and whether or not they will be useful for the job in hand and finally whether or not he can get it in tube form.
Depending on whos serious about trying to get these made up surely we could a discount on some good quality rosejoints if we bought them in bulk??
The question i have is if i were to run the adjustable rear linkage what arb would be used and how would it be fitted?? I have a MK4 popular so i dont have a rear arb to start with.
This might be a stupid question but is there any alternative to using rosejoints??
If you get some measurements etc, i'll CAD bitch up some drawings, and maybe rune some stress analysis if i can work out a realistic load.
I was also thinking last night, the rear tie bars won't be massively loaded compared with the rear lower arm i don't think.... (could be wrong) but i think they will be subjected to compressional loads rather than a bending load? so ali could be used here and maybe mild steel for the lower arm(s)?
Rob,
#70
Wye Valley Hardcore

I was also thinking last night, the rear tie bars won't be massively loaded compared with the rear lower arm i don't think.... (could be wrong) but i think they will be subjected to compressional loads rather than a bending load? so ali could be used here and maybe mild steel for the lower arm(s)?
Rob,
Rob,
Standard tie rods have broken on numerous occasions. Whether its down to poor quality steel used by Ford, or wear and tear being old I'm not sure, but the load on it would probably be more than you think IMO. Especially if you wanted to run toe in/toe out that part would be under a pulling or pushing load on the rear hub? How much force I wouldn't be able to say, thats not my area lol
Its nice to see a proper topic in this section for a change where we are actaully thinking about the materials, loads, weights etc and having a proper discussion, rather than bickering over nonsense.
#71
I'm Finding My Feet Here Now
Thread Starter
Join Date: Nov 2009
Location: Hertfordshire
Posts: 101
Likes: 0
Received 0 Likes
on
0 Posts

Point taken muz feels like a proper brainstorming thread with ideas bouncing around everywhere!!
Ruby123 is there any chance of you taking some measurements of the kit you've got so we've got an idea on how much material would be needed.
Also since theres been a great deal of talk about the overall weight of the components could stick the whole box on a set of scales so we actually have a rough idea of how much it will weigh and then whether or not it will be cost effective to use aluminium as apposed to CDS.
Any idea what material was actually used for your setup aswell as that would help also.
Rob i can only seem to find the figures for yield and tensile strength of CDS or ali cant seem to find anything on compression strength. How to you go about finding out the stress loads anyway.
Correct me if im wrong muz but are the standard tie bars cast iron?? they just seem realli heavy and not made with a great deal of precision, and rob's idea of using mild steel for the tie rods and maybe ali as the trailing arms is a great idea as CDS will probably be more than up to the job.
Also everyones been debating whether to used solid rod or tube, if the rs1600i arb i have is made from alloy tube then it must be strong enough and i cant imagine ford would have spent a fortune on expensive alloy so i dont think that is as big of an issue as originally thought.
Ruby123 is there any chance of you taking some measurements of the kit you've got so we've got an idea on how much material would be needed.
Also since theres been a great deal of talk about the overall weight of the components could stick the whole box on a set of scales so we actually have a rough idea of how much it will weigh and then whether or not it will be cost effective to use aluminium as apposed to CDS.
Any idea what material was actually used for your setup aswell as that would help also.
Rob i can only seem to find the figures for yield and tensile strength of CDS or ali cant seem to find anything on compression strength. How to you go about finding out the stress loads anyway.
Correct me if im wrong muz but are the standard tie bars cast iron?? they just seem realli heavy and not made with a great deal of precision, and rob's idea of using mild steel for the tie rods and maybe ali as the trailing arms is a great idea as CDS will probably be more than up to the job.
Also everyones been debating whether to used solid rod or tube, if the rs1600i arb i have is made from alloy tube then it must be strong enough and i cant imagine ford would have spent a fortune on expensive alloy so i dont think that is as big of an issue as originally thought.
Last edited by Project_Bonus; 21-10-2011 at 11:22 AM.
#72
Too many posts.. I need a life!!
iTrader: (2)

I'll find them out later also on the rose joints how I understand them they are not a fit and forget item and won't last for ever so if they are an item that will be swapped every x amont of miles /years its may not be cost efective to go for Ł50 rose joints over mid range ones
#73
Wye Valley Hardcore

They could well be, I've never really looked at them to be honest. The best thing you can do is reduce unsprung weight so if you could use Aluminium for some or all of it would be a plus (permitting that threading the ally is strong enough, I would not like a joint to pull the thread out on track!), but if it's Ł100 more expencive to save 1 kg a side, I'd rather just use CDS.
Last edited by muz; 21-10-2011 at 11:26 AM.
#74
PassionFord Post Whore!!
iTrader: (4)

Rob i can only seem to find the figures for yield and tensile strength of CDS or ali cant seem to find anything on compression strength. How to you go about finding out the stress loads anyway.
TBH i think material choice is less important than we think (as in weight saving is less important than say... a lower arm snapping at 100mph half way round a corner). My first choice would be mild steel, easy to weld, buy etc etc and if all goes well then perhaps look at ali as a future weight saving alternative...?
Muz, fucking good point mate, i completely blanked all the threads i've read about broken tie bars lol which i guess does imply more load than i was thinking.
The other thing that bugs me is the little kink in the tie bar,
I guess if a straight tube was used the rose joint at the front (in place of the bush) would allow the bar to sit at an angle, meaning the kink wouldn't be needed to clear anything etc...?
Then i found these, which are for a mk5 escort, but they looked cool enough to post up

Also found this thread with some more helpful pics
https://passionford.com/forum/ford-e...bar-setup.html
Rob,
Last edited by Rob_DOHC; 21-10-2011 at 12:55 PM.
#75
PassionFord Post Whore!!
iTrader: (4)

How to you go about finding out the stress loads anyway.

The suspension is a system with numerous items sharing loads, so in theory if you sat down and pulled out an old GCSE text book you could easily work out the loads applied to various parts AT REST as long as you knew angles of suspension components etc, but that doesn't help us in the real world. First you have to know what load you are applying, you could probably make good estimates by using the loads at rest and adding the additional 'extra loads' of a moving vehicle......
What you need to do is work out the peak load an item will see, then add a decent safety margin. So maybe double the load and THEN look at materials that are suitable.
I use solid works for this (on single components) to look at deformation at certain loads.
IMO a road car see's far higher stresses than a track car, suspension wise.
Rob,
Last edited by Rob_DOHC; 21-10-2011 at 12:56 PM.
#76
Wye Valley Hardcore

TBH i think material choice is less important than we think (as in weight saving is less important than say... a lower arm snapping at 100mph half way round a corner). My first choice would be mild steel, easy to weld, buy etc etc and if all goes well then perhaps look at ali as a future weight saving alternative...?
Muz, fucking good point mate, i completely blanked all the threads i've read about broken tie bars lol which i guess does imply more load than i was thinking.
The other thing that bugs me is the little kink in the tie bar,

I guess if a straight tube was used the rose joint at the front (in place of the bush) would allow the bar to sit at an angle, meaning the kink wouldn't be needed to clear anything etc...?
Then i found these, which are for a mk5 escort, but they looked cool enough to post up
, MUCH more expensive to make though. But there may well have been a good reason to use solid ali rather than a thin(ish) wall ali tube.....

Also found this thread with some more helpful pics
https://passionford.com/forum/ford-e...bar-setup.html
Rob,
Muz, fucking good point mate, i completely blanked all the threads i've read about broken tie bars lol which i guess does imply more load than i was thinking.
The other thing that bugs me is the little kink in the tie bar,
I guess if a straight tube was used the rose joint at the front (in place of the bush) would allow the bar to sit at an angle, meaning the kink wouldn't be needed to clear anything etc...?
Then i found these, which are for a mk5 escort, but they looked cool enough to post up

Also found this thread with some more helpful pics
https://passionford.com/forum/ford-e...bar-setup.html
Rob,
The joints at each end would allow the bar to be straight and get rid of the kink.
#77
Too many posts.. I need a life!!
iTrader: (2)

The link bars are 37cm long the tie bar length are obviously dependant on what end design you go for the ones I've got use the standard bush and are 49.5 cm long go were the washer would sit as standard I was told not to use rose joint on both ends as what was about at the time fitting wise didn't let it move as it should
#78

Very interesting thread this, I have a couple of MEF copied rear adjustable arms in Ally I got off ebay, but wasn't too sure of the strength so haven't fitted them. They seemed too flimsy to me.
#79
Wye Valley Hardcore

The Group A cars also seem to use a much different rear ARB. Whether this was because the original cars didn't have one as standard or they were simply much better I'm not sure? If I were going to make new multi link, I'd proabbly replicate a Group A ARB and make the whole suspension set up Group A.
Brooklin ECS Group A RS1600i


Datapost 77 Group A RS1600i


Brooklin ECS Group A RS1600i


Datapost 77 Group A RS1600i


